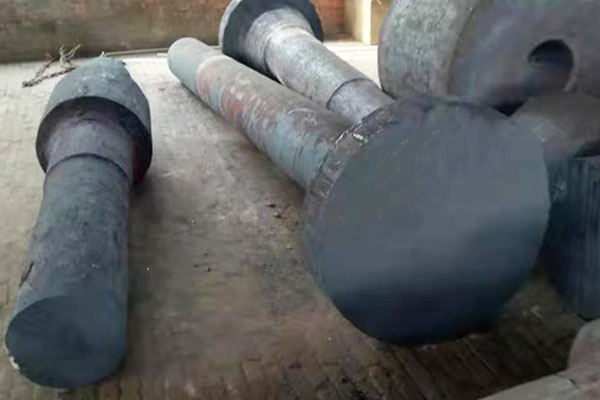
自由鍛件余熱淬火
⑴ 穩(wěn)定可控的加熱體系。坯料的加熱體系為中頻感到加熱、紅外測(cè)溫儀和三通道溫度分選體系,可利便的掌握加熱溫度和分選加熱溫度分歧格的坯料。
⑵ 確定合適的淬火溫度,并能有用加以掌握。合適的鑄造余熱淬火溫度需憑據(jù)實(shí)驗(yàn)確定,現(xiàn)實(shí)操縱中可通過掌握鑄造加熱溫度、鍛后停頓時(shí)間來實(shí)現(xiàn),鍛后停頓時(shí)間推薦碳鋼不大于60s、合金鋼在20~60s之間。
配置紅外測(cè)溫儀和溫度分選體系,將低于淬火溫度的鍛件分選出去;當(dāng)鑄造加熱溫度穩(wěn)定、鑄造歷程也穩(wěn)定時(shí)可配置工序時(shí)間測(cè)量和報(bào)警體系,通過掌握工序時(shí)間到達(dá)掌握淬火溫度的目標(biāo)。
⑶ 良好的淬火體系。在包管淬火結(jié)果的條件下選定冷卻才氣較慢的淬火劑,以防備緊張淬火變形和開裂。因?yàn)殍T造余熱淬火溫度比一般淬火溫度高,是以鍛件淬透性好,故碳鋼和合金鋼一般選用油或PAG淬火劑。
淬火槽應(yīng)有足夠的容積,冷卻時(shí)間可控,另外還要配置淬火介質(zhì)輪回、冷卻體系和加熱裝配,淬火介質(zhì)溫度自動(dòng)掌握,還應(yīng)配置抽風(fēng)裝配。增強(qiáng)對(duì)淬火介質(zhì)的保護(hù),定期檢驗(yàn)淬火介質(zhì)的冷卻性能,清理液槽及輪回體系中的氧化皮等雜質(zhì),保持淬火介質(zhì)的潔凈。
⑷ 淬火后的回火和回火爐的配置位置。鍛件淬火后其里面存在較大應(yīng)力,造成放置歷程中產(chǎn)生較大變形乃至開裂。為防備淬火后零件變形和開裂,淬火后鍛件應(yīng)實(shí)時(shí)回火。鍛件淬火后可棄捐時(shí)間與鍛件質(zhì)料、形狀和環(huán)境溫度相關(guān),需憑據(jù)實(shí)驗(yàn)確定。為勤儉動(dòng)力和進(jìn)步回火爐的行使率,降低保溫能耗,接納余熱淬火的鍛件一般在熱處分車間密集回火。
鍛件廠家直銷哪家好,就找唐山盛通鍛造有限公司。
Free forging quenching
(1) Stable and controllable heating system. The heating system of the billet is a medium frequency sensing heating, an infrared thermometer and a three-channel temperature sorting system, which can conveniently grasp the billet of the heating temperature and the sorting heating temperature.
(2) Determine the appropriate quenching temperature and be useful to grasp. The suitable quenching temperature of casting residual heat should be determined by experiment. In reality, the casting heating temperature and the dwell time after forging can be realized. The post-forging pause time is recommended to be no more than 60s for carbon steel and 20 to 60s for alloy steel.
The infrared thermometer and the temperature sorting system are arranged to sort out the forgings below the quenching temperature; when the casting heating temperature is stable and the casting process is stable, the process time measurement and alarm system can be configured, and the quenching temperature can be grasped by mastering the process time. The goal.
(3) Good quenching system. Under the conditions of the quenching result of the tube, the quenching agent with a slower cooling gas is selected to prevent the tension quenching deformation and cracking. Because the quenching temperature of casting residual heat is higher than the general quenching temperature, the forging is good in hardenability, so carbon steel and alloy steel are generally selected from oil or PAG quenching agent.
The quenching tank should have sufficient volume, the cooling time can be controlled, and the quenching medium recirculation, cooling system and heating assembly should be arranged. The quenching medium temperature is automatically mastered, and the exhaust assembly should also be configured. Enhance the protection of the quenching medium, regularly check the cooling performance of the quenching medium, clean the impurities such as scale in the liquid tank and the recirculation system, and keep the quenching medium clean.
(4) The location of the tempering and tempering furnace after quenching. After the forging is quenched, there is a large stress inside it, which causes large deformation and even cracking during the placement process. In order to prevent deformation and cracking of the parts after quenching, the forgings after quenching should be tempered in real time. After the forging is quenched, the time of donation can be related to the material, shape and ambient temperature of the forging. It needs to be determined by experiment. For the diligent power and progress of the tempering furnace, the insulation energy consumption is reduced, and the forgings that receive the residual heat quenching are generally densely tempered in the heat treatment workshop.
0315-3172368
熱線電話
關(guān)注官方賬號(hào)